05 November 2024
Subsea Pinpointing
The Pinpointing project enhances offshore cable fault detection, reducing downtimes and losses with advanced technologies in marine surveying and fault location.
Context
The Pinpointing project is essential to improve the accuracy of offshore cable fault detection. Precise fault localization minimizes asset downtimes and repair costs, ensuring a more reliable and efficient offshore energy transmission system. By leveraging advanced technologies, this project enhances operational efficiency and supports the uninterrupted delivery of renewable energy from offshore sources.
Approach
To ensure the success of the Pinpointing project, we are adopting a multi-phase, collaborative approach. The project begins with a thorough study of existing cable fault detection technologies, followed by the development of a testing framework that includes fault simulation systems. We are leveraging both controlled wet test environments and real-world offshore conditions to refine and validate the accuracy of these systems.
By partnering with leading marine and technology experts, we aim to combine state-of-the-art pinpointing techniques with advanced fault simulation methods. This iterative testing process allows us to gather critical insights, optimize system performance, and ensure that the pinpointing technology can withstand challenging offshore conditions. Additionally, we are working towards setting new industry standards for fault location accuracy and system resilience, laying the groundwork for future commercial solutions that will benefit the entire offshore energy industry.
Results
In the first stage of the Pinpointing project, we carried out extensive research to understand the different types of faults that can occur in submarine cables and the most effective ways to detect them. Here's what we've discovered so far:
-
Types of Submarine Cable FaultsOur research identified that submarine cables can suffer from various types of faults caused by mechanical stress, chemical corrosion, thermal stress, and electrical stress. These stresses can lead to immediate short circuits, long-term degradation, or faults in cable accessories.
-
Detection MethodsWe reviewed state-of-the-art technologies and methods for detecting and pinpointing cable faults like time domain reflectometry (TDR), frequency domain reflectometry (LIRA) and optical time-domain reflectometry (OTDR). Especially OTDR showed significant promise since a lot of development is happening and it allows us to monitor cable conditions continuously and detect potential issues before they escalate into major problems.
-
Technology EvaluationWe evaluated the accuracy and reliability of different pinpointing technologies using interviews and literature references. For example, methods such as Line Impedance Resonance Analysis (LIRA) and Brillouin OTDR were found to be effective in locating faults and weak points within a range of 10 to 20 meters for cables up to 150 kilometres long.
-
Industry CollaborationThroughout the research phase, we collaborated with INP Greifswald and the University of Rostock, both leading research institutions in the fields of physics, electrical engineering and maritime environments. We conducted interviews with other TSOs and many technology providers and compiled it for the future project execution.
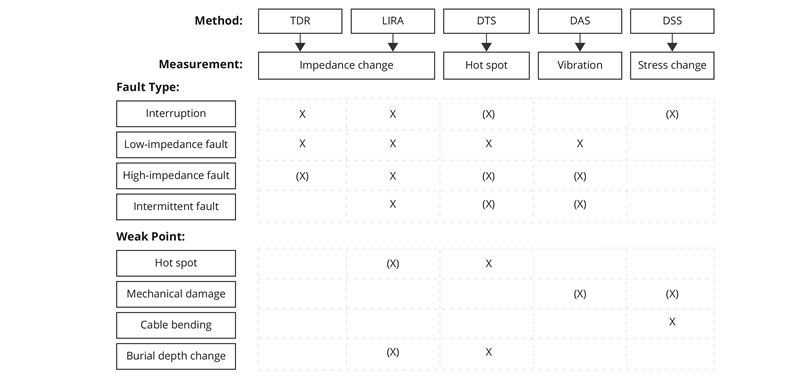
Key Steps in the Troubleshooting Process:
-
Cable InstallationInitiating the troubleshooting process during installation is crucial. Integrating monitoring systems at this stage to perform fingerprints and establish baselines helps identify manufacturing or handling faults early on.
-
Cable OperationContinuous non-invasive monitoring using technologies such as DAS (Distributed Acoustic Sensing) and DTS (Distributed Temperature Sensing) is essential for detecting weak points that could lead to faults during operation.
-
Fault DetectionAutomated systems generate alerts for faults, which can indicate trivial issues or signal the need for further investigation.
-
Fault IdentificationOnce detected, analyzing the fault's nature allows for targeted action. Impedance measurements can identify specific affected components.
-
Fault Pre-location
This stage involves narrowing down the fault's location. We differentiate between:
- Non-invasive Pre-location: Utilizing ongoing monitoring data.
- Invasive Pre-location: Conducted after service interruption, applying controlled excitation methods for better accuracy.
-
On-site Fault PinpointingIf previous methods fail, precise localization requires specialized equipment and is undertaken only when necessary.
Next steps
Based on the insights gained from the first work package (WP1) and market evaluations, the team has decided to move forward with Distributed Acoustic Sensing (DAS) technology for pinpointing subsea cable faults. This choice is driven by DAS's promise to use existing optical fibres in power cables for accurate fault detection. The important innovation here would be to enhance DAS’ accuracy using a precise georeferencing exercise, which is something that needs to be validated through extensive testing. Here’s how we plan to advance the project:
-
Engineering and Development (WP2)
- Develop a submergible, waterproof fault simulator to generate acoustic signals mimicking power cable discharges. The fault simulator should be able to interact with a DAS system, even through 1-2 m of sand.
- Develop a precise georeferencing process and the necessary software to make use of georeferenced data. The goal is to enhance standard DAS practices and gain the required precision for pinpointing.
-
Wet Testing (WP3)
- Conduct initial trials in controlled environments, such as basins or ports, using optical fibre cables to simulate submarine power cables.
- Ensure the fault simulator can function effectively under various maritime conditions and can be buried, repositioned, and recovered.
-
Field Testing (WP4)
Validate the functionality of the DAS system and fault simulator with real subsea power cables by
- Performing a georeferencing exercise.
- Use an ROV with the signal generator to simulate cable faults
- Use the georeferenced data and DAS signals to accurately predict the fault location.
-
Georeferencing for Real-Life Campaigns
- Plan georeferencing campaigns by mounting signal generators on remotely operated vehicles (ROVs) to map existing cables.
- Integrate this data into our IT infrastructure to enable real-time fault location predictions during actual faults using DAS systems.
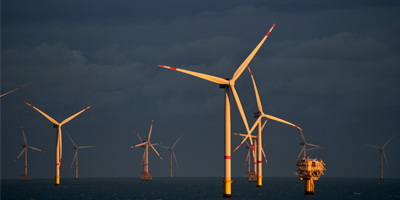