28 December 2022
Unmanned Surface Vehicles and offshore O&M activities
First test of USV to inspect offshore transmission assets 40 km off the Belgium coast in the North Sea
Context
In November 2020, the EU published its Offshore Renewable Energy Strategy (ORES), outlining its goal to increase Europe’s offshore wind capacity from 12 GW to 300 GW by 2050.
In May 2022, Belgium, Denmark, Germany, and the Netherlands signed the Esbjerg Declaration at the North Sea Summit, during which they committed to jointly reaching 150 GW of offshore wind generation capacity by 2050.
As Transmission System Operator’s, the role of Elia Group and its subsidiaries, Elia(Belgium) and 50Hertz (north-east of Germany) is to transport and integrate the electricity generated at sea to the onshore grid.
Whilst the energy transition brings many opportunities with it, such as reaching the targets of the EU’s green deal and enhancing European energy security, offshore wind projects and their value chains also carry several challenges.
Offshore, by definition is cost intensive and related to safety risks. For operations and maintenance (O&M) activities that prolong the life of offshore assets, the cost and risk are significantly higher than for onshore projects. With corrosion due to the water salinity, seabed movements, weather and wave conditions that reduce access and flexibility, offshore O&M activities require highly trained staff for various operations.
To inspect its subsea cables and offshore platforms, Elia Group’s staff deploy a whole variety of survey and support vessels to undertake bathymetric surveys (mapping of depths and shapes of underwater terrain) with equipment including remotely operated vehicles (ROVs), and all different types of sonar systems. These are used to determine whether the assets have encountered any issues, such as damage to the structure integrity and whether the subsea cables are still buried at the right depth.
Unmanned Surface Vehicles, also known as USVs that can carry the necessary sensors and be operated remotely from an onshore base, therefore have a lot of potential. Their adoption and regular use could increase the efficiency and flexibility of inspections while substantially reducing the safety risks, dependence on the weather, environmental impacts, and cost of offshore O&M activities.
As part of its goal of moving from curative (or reactive) to predictive and condition-based maintenance to minimize asset downtime or failure and maximize system availability, Elia Group undertook a proof of concept (PoC) to test the potential of USVs and their role in supporting offshore O&M activities.
Approach
As part of the PoC, Elia Group tested Tupan, an USV that was designed and built by TideWise (the winner of the Elia Group Open Innovation Challenge 2021). Tupan is five meters long, weighs about 1500 kg, has a top speed of 6 knots, maximum endurance of 12 days, can carry several sensors to inspect offshore assets and collect mid-ocean data. Tupan can be operated either autonomously or remotely with a hand console.
The objective of the PoC was to assess the maturity and feasibility of inspections carried out with remotely operated/autonomous USVs. This was done by undertaking a survey of the subsea cables of Elia’s Modular Offshore Grid’s (MOG) and inspecting its Offshore Switchyard (OSY), which lies 40 km out of the Belgian coast. The validation criteria included security and feasibility in terms of operations and permission processes; output quality of the inspection; sustainability in terms of CO2 emissions; and cost.
For the test, the USV was equipped with the following:
- a MBES sonar system, to make a high-resolution cartography of the seabed and assess the burial depth or protection status of our submarine cables;
- a LiDAR laser scanning system, to create a detailed 3D model of the OSY topside and jacket structure above the waterline;
- a drone platform with a high-resolution camera attached, to inspect and detect any damage along the OSY platform.
Scope of the PoC was to depart from the port of the Blankenberge, survey the cable route (~40km) with the MBES, cross the dense shipping lane of Het Scheur, and inspect the OSY Platform using a LiDAR laser scanner and drone with a high-resolution camera.
Results
The USV completed the survey activities in site conditions of up to 1.5m maximum wave heights, providing accurate and high-resolution seabed data from the sensors mounted on the USV, in water depths from 0 till 35 meter. The test’s preliminary results in terms of the validation criteria are outlined below.
Regarding security and feasibility: During the test, no incidents, HSE accidents or near misses occurred. Under current legislations' USV’s cannot operate fully autonomous or remotely in open waters off the Belgian coast. Therefore, with support from Dries Boodts of the MRCC (Shipping Assistance Division of Belgium Cost Guard) and Jean-Baptiste Merveille from DG Shipping, the USV was followed by a support vessel at all times to ensure safety and security throughout the PoC.
Regarding output quality: In the bathymetry model of the seabed surface that the USV collected, it is possible to identify sand waves; dynamic features of the seabed such as mega ripples; cable fixation structures; and footprints left by dredging and trenching from the cable installation phase (see image 3). The LiDAR scan produced a high-resolution model with sufficient points per square meter/m2 of the OSY to create an accurate 3D model of the structure. The drone produced high-resolution video footage of the OSY, enabling the detection of possible damage and corrosion.
Regarding sustainability: A survey mission with an USV can reduce fuel consumption and the amount of CO2 emissions per hour by over 98% when compared to a mission with a survey vessel.
Regarding cost: With large reductions in fuel consumption and a reduced need to plan for trained staff to go offshore, USVs promise to substantially reduce the costs associated with inspection surveys.
Next steps
The PoC has demonstrated that USV’s have reached the maturity to support offshore O&M activities. Further tests are necessary to validate the development and system integration, explore operational challenges and develop a regulatory framework for using USVs offshore.
For more information, you can watch the project video
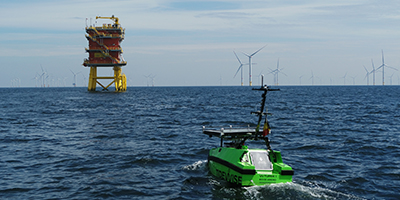