16 January 2023
Acoustic sensors to monitor critical assets (OIC 2019)
The NEMO Link converter station connects the electricity system of Belgium and Great Britain via subsea cables.
Why this project
The cooling systems of the converters ensures its safe operation. This already closely monitored cooling system serves as an ideal reference system to test a new type of sensors in a challenging environment. The goal of this POC is to understand if the sensors in combination with the Artificial Intelligence (AI) algorithm can provide additional health indicators to complement the existing monitoring and alert system. Beside the capability of the algorithm, we give answers to practical questions of mounting the sensors, ensuring stable operation and safe data transmission.
Approach
Three phases define this proof of concept:
- Firstly, a feasibility study describes the possibilities as well as the limitations of the project.
- In the second phase, the sensors to start collecting acoustic samples. Those samples cover typical operational modes of the system. That information enters a deep learning algorithm and together with Nemo Link experts, OKTO Acoustics trains its algorithm to define a healthy operation mode. Special attention is given to the cooling pumps that undergo the first maintenance interval during the POC. Differences before and after those measures shall deliver valuable insights on the status of the asset.
- In the last project phase, the monitoring system will go in live operation mode.
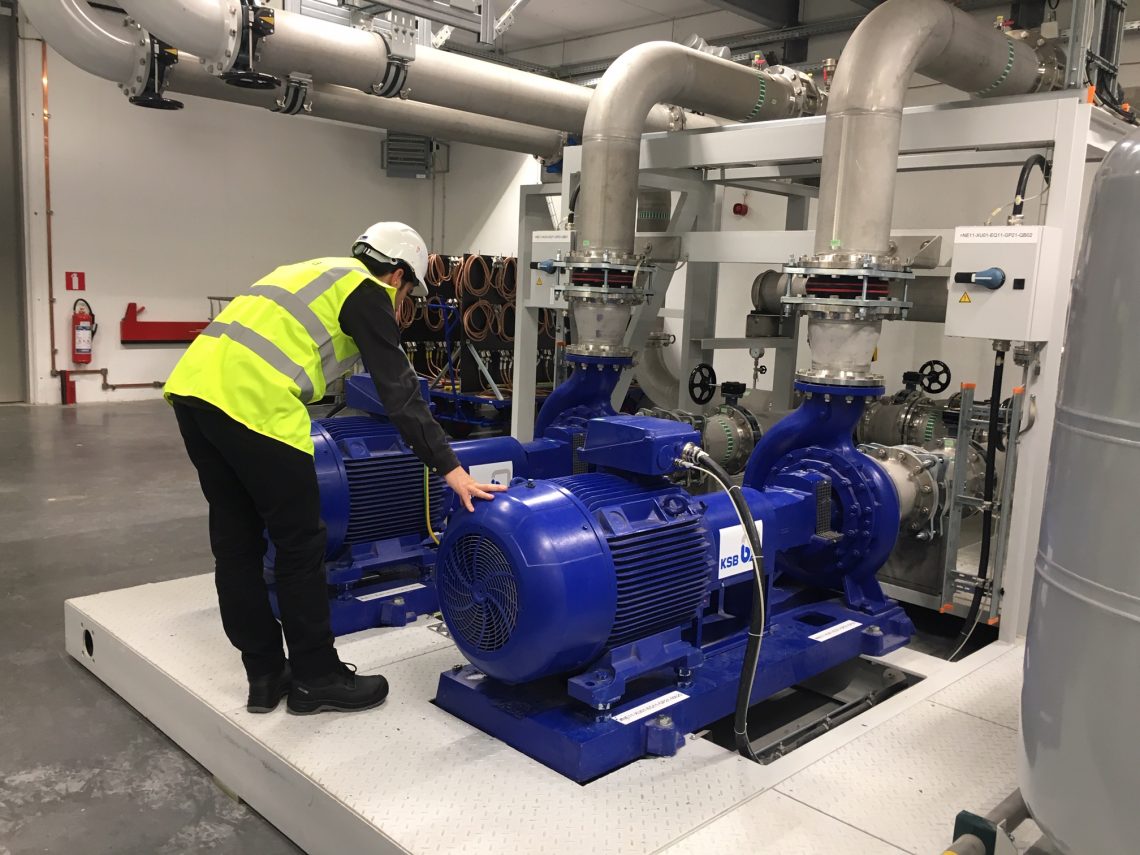
-
Mounting of sensorsOKTO Acoustic developed custom-made mounts to attach the sensors on the assets of the cooling system. The special environment is adding another layer of complexity to this project.
-
Training the algorithmAutomatic detection of unhealthy operation or faults requires the sampling of those cases. Since this is not possible for a system in operation, the analysis is based small deviations in the sound spectrum before and after maintenance measures. Additionally the neural network is trained on the different standard operation modes of the cooling system such as pump switches and different valve positions. Operational log files serve as a basis and Nemo Link’s technical experts provide expertise that allows OKTO Acoustics to train the algorithm ex-post and to prepare for live operation.
-
Live operationAfter training of the basic operation modes, the system goes into live operation. The system needs to prove its capability of providing the current operation mode and the state of each monitored asset out of the complex set of information. In case the system proves to operate successfully, Nemo Link is considering a long-term test of the smart sensors.
Results
The technology has proven its potential
With the installation of acoustic sensors on the cooling pumps at the Nemo Link converter stations in Zeebrugge (Belgium) and Richborough (UK) in October last year, OKTO Acoustic started to test their AI-based system on Nemolink assets. The solution successfully proved its potential to provide a health indication by “listening” to the acoustic information emitted from the bearings of the pump during operation. Since the technology caught the attention of transformer experts during its presentation at our innovation week in December, a new use case has been identified and is currently tested in Belgium
This non-intrusive method captures the acoustic information from bearings and analyses their condition close to real time for all of the 8 pumps. This condition state information (on/off status as well as health indication) is accessible through an online user interface. To get there, the experts from OKTO Acoustics trained their algorithm with acoustic samples recorded from their sensors and combined it with information from Elia experts. With the help of the analysis, the unique acoustic spectrum and the emitted acoustic energy of each of the pumps became visible. The sensors have on board microprocessors that are now able to process and label the acoustic pattern while filtering irrelevant background noises. The results show substantial differences between the pump’s acoustic signatures and the experts identified the critical frequency bands in which wear and tear becomes noticeable.
Nevertheless, there are still some hurdles to take before such a system could be brought into full operation and provides actionable insights to the operators and engineers. To give a reliable indication on the state of a bearing, the ground truth under the format of an acoustic signature of a new and healthy bearing (and ideally of a worn out one as well) is required. Under the assumption that this data is available, also a threshold for critical acoustic spectrum deviation should be defined as from which the system should raise a warning or even an alarm to the operators and engineers. Further, it is an open question how scalable the system behaves when being applied to similar pumps at other converter stations.
The technology is developing towards industrialization and has proven its potential. The sensors can be applied for a wide spectrum of usecases and we are continuing to explore their capabilities.
Partners
![]() |
![]() |